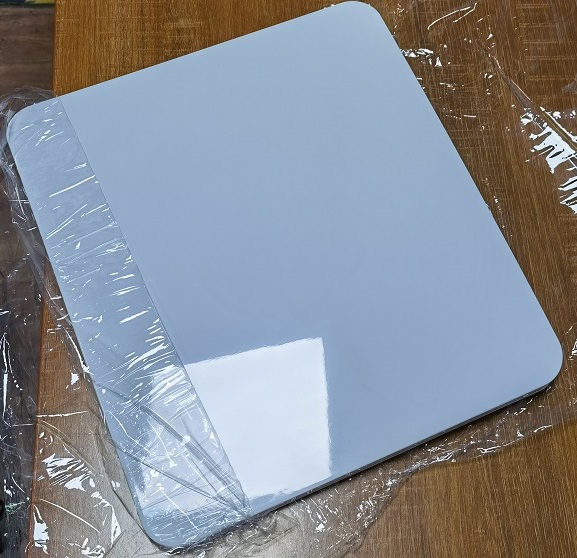
Sometimes we may need to make the mold “inverted”.
What is an “inverted mold”? “Inverted mold” means,
- core inserted in the A plate, cavity in the B plate.
- the injection system and the ejector system are located in the same side.
- usually with hot runner.
Why do we need “inverted mold”?
Let’s take this project as an example. Please see the photo below,
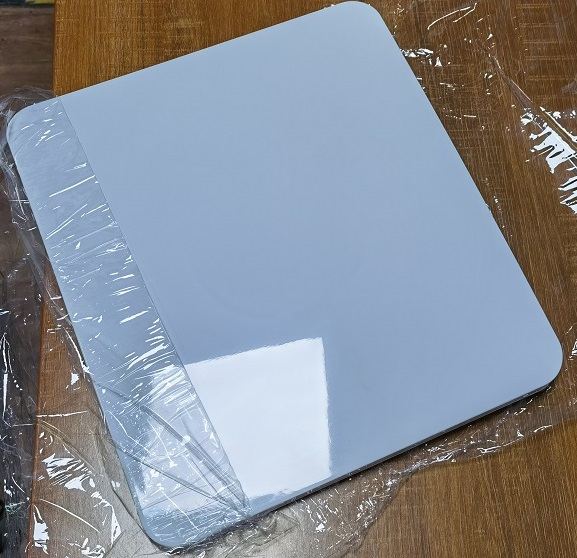
You see, the customer need high-glossy surface, and don’t permit any injection gates in the visible surface.
So, the best solution is making the mold “inverted”.
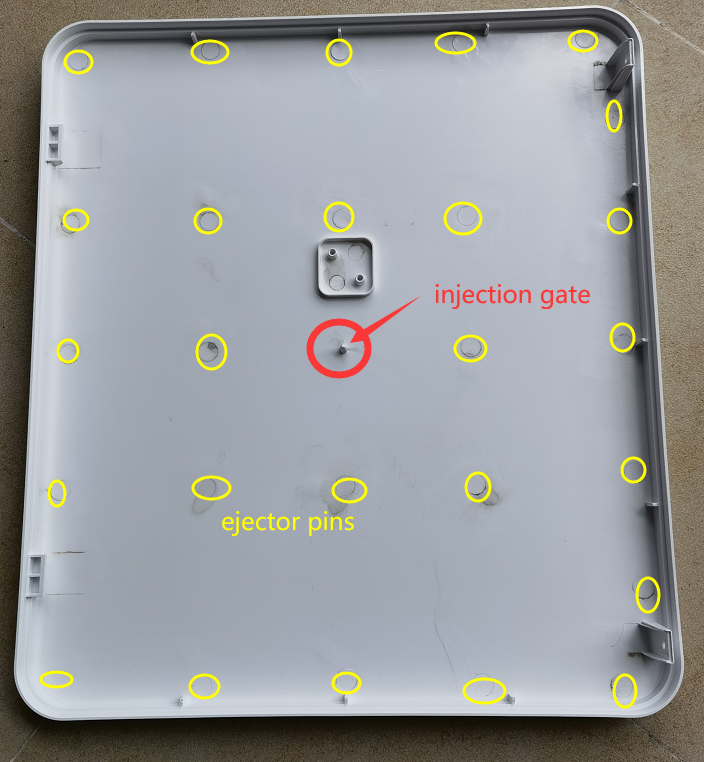
(you see, injection gate is in the same side as ejector systems.)
By doing it, we can achieve both goals at the same time:
- inject from the in-visible surface &
- ejector from the in-visible surface.
This can optimize the surface to a great extent.
“Inverted mold” is good. However, the cost is usually high.
From the very beginning, our customer thought of 3-plate mold with 2 sub-gates / 4 sub-gates.
So we made the mold-flow according to their requirement,

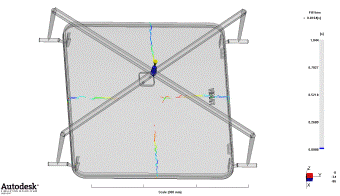
And when we suggested #invertedmold to this customer, they didn’t accept the extra-cost.
And then, we re-did the mold flow based on “inverted mold” as below,
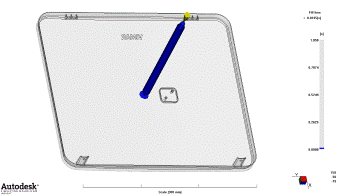
Till this stage, our customer still didn’t accept the “inverted mold” because of the extra-costs.
We told them that the extra cost is cuased by,
- different mold structure
- hot runner
Finally, they said yes.

This “invertedmold” was received by our customer 5 years ago.
They are much satisfied with our professional skills, our service, and our competitive prices.
By Fredrick Hempstead (eg101@egtooling.com) from E G Enterprise Limited.
All rights reserved.